As consumer demand for sustainable, affordable housing outpaces conventional construction capacity, mass timber and modular building are increasingly viewed as promising solutions. Now, global leader in prefabricated solutions Lida Group unveils plans to merge these innovations through development of a groundbreaking Hybrid-CLT container home community targeting 50% savings over traditional site-built homes.
Announced today, the 100-unit complex represents a first-of-its-kind hybrid building system integrating mass plywood and glue laminated timber (CLT) structural framing within standardized steel shipping container modular components. Offsite container construction andCross-Laminated Timber (CLT) framing aim to deliver a highly efficient, durable and cost-competitive housing option supporting adoption of greener building methods.
“By combining the benefits of mass timber and modular building, we believe Hybrid-CLT construction can make sustainable housing attainable for many more families,” explained Lida Group CEO Mu during groundbreaking. “Early studies indicate the design may reduce overall construction costs by 50% versus typical site-built homes.”
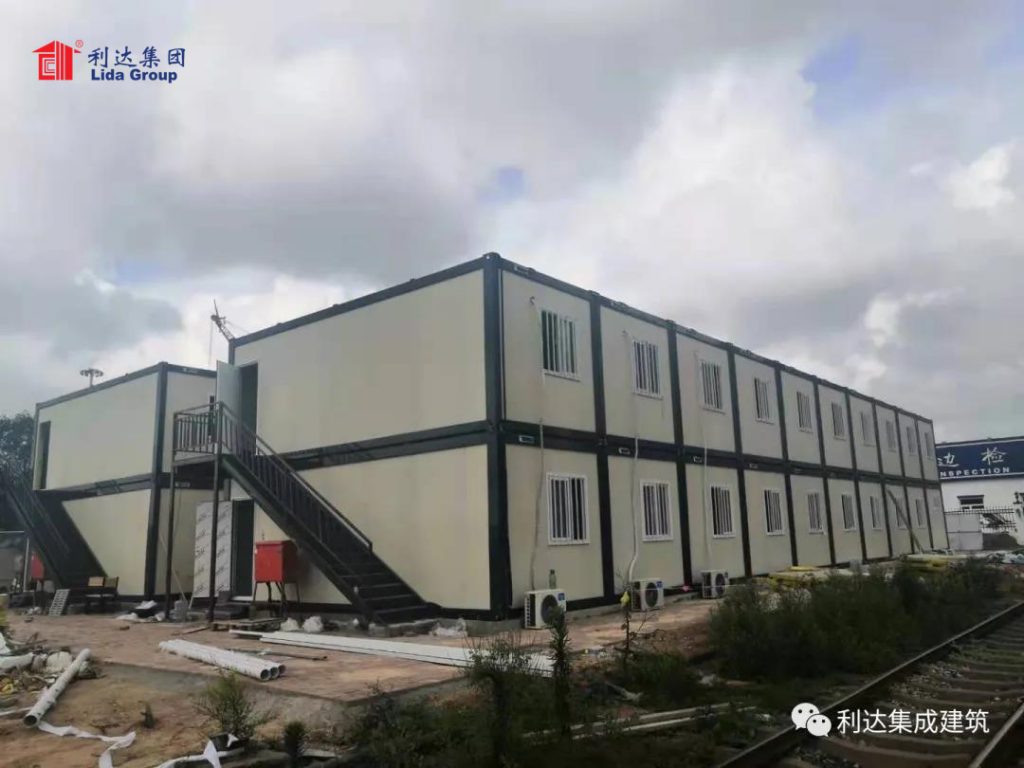
flatpack container house
3D engineering simulations first evaluated assembling essential living spaces within steel shipping container modules, with CLT constructed “connective tissue” linking dwellings. Progressing to a full-scale prototype validated the hybrid concept’s structural integrity far exceeding code requirements at reduced material usage.
On automated production lines established near sustainably managed forests, 5-axis CNC machining cuts interlocking mass timber components like wall,floor and roof panels with industrial precision. Robotic arms complete MEP subsystem installations within prefabricated container pods. Entire living modules undergo testing and inspection off-site before delivery.
At the development site on the outskirts of Guangzhou City, reinforced concrete foundations with post-tensioned tie-downs receive CLT-framed modules. Mass timber structural “spines” channel utilities efficiently throughout, while modular units retain flexibility to rearrange or expandliving configurations spatially as needs evolve over long building lifecycles.
Ongoing research with Hong Kong University assesses Hybrid-CLT construction’s whole-lifecycle sustainability and carbon footprint. Early findings indicate dramatically reduced operational energy usage through superior thermal mass and airtightness. Recyclable or reusable components at end-of-life further enhance environmental advantages of the design.
If successful, experts foresee the Hybrid-CLT system enabling production of affordable housing at an unprecedented 35 units monthly. Wider adoption promises to boost mass timber markets while further advancing modular construction’s scalability. For consumers, it presents the attractive package of sustainable, durable and cost-competitive housing.
With this pilot development, Lida Group aims to validate Hybrid-CLT construction’s feasibility to radically transform the supply-demand imbalance challenging construction industries and communities globally through green and efficient mass production techniques.
In summary, through merging mass timber and modular construction innovations, Lida Group’s Hybrid-CLT complex pioneer a breakthrough building system empowering widespread green housing delivery at competitive costs with industrialized efficiency. If projections hold true, Hybrid-CLT construction may revolutionize construction industries’ sustainability and affordability.
Related news
-
New research collaboartion between Lida Group and university exploring ways to optimize design and assembly of multifamily apartments constructed using recycled steel shipping containers aims to radically reduce costs of urban housing
2023-10-30 16:38:42
-
Resident-First Mobile Living: A Look at the Features and Amenities Lida Group Integrates Based on Real Feedback to Consistently Deliver Lifelike Temporary Housing Experiences
2023-10-27 15:27:04
-
Working Wonders Under Pressure: How Lida Group Excels at Delivering Robust Temporary Housing Infrastructure for Industries' Tight Timelines Through Modular Coordination and Standardized Processes
2023-10-27 14:32:40
contact us
- Tel: +86-532-88966982
- Whatsapp: +86-13793209022
- E-mail: sales@lidajituan.com